Axial Reactor Internals
Woven Metal Products (WMP) has been servicing axial flow reactors and supplying companies with needed internals for decades. Axial reactors, also called downflow reactors, refer to the flow direction inside the vessel, in this case, along the vessel axis.
In most cases, catalyst is filled to a certain height and the liquid or gas flow is either upwards or downwards. In any axial flow reactor, the components are critical to ensure catalyst retention, allowing for superior process flow and maximum output.
Products we manufacture for axial flow reactors include:
Catalyst Support Grids
WMP support grids offer superior media containment and process improvement solutions for many applications including hydrotreaters, hydrocrackers, molecular sieves, horizontal sulfur recovery units, adsorption units and many others. We manufacture all types of support grids to exact specifications.
Types of catalyst support grides we offer include:
WMP Outlet Support Grid (OSG):
WMP’s patented proven support grid system combines years of research and development efforts with the latest fabrication techniques to deliver a world-class solution for many applications, providing excellent ROI. The WMP OSG allows for:
-
- Superior hydraulic catalyst bed manipulation
- Critical catalyst bed containment
- Additional catalyst bed depth, gained by utilizing the vessel head for support allowing this unit to be installed below the vessel tangent line
- De-bottlenecking, often providing vessels with additional bed capacity in some applications up to 40% additional bed depths can be realized
- Easy installation, making this a wise selection for turnaround planning
- Can easily pass through the existing manway to fit any process application
- Can be easily removed in sections or the entire unit, facilitating easier inspection, cleaning or repair
- Offered in a variety of material options, offering years of worry-free operation
Catalyst Support Grids:
Matching the support system to the grid is an integral piece of fabrication and installing components. Catalyst Support Grids from WMP offer the following benefits:
-
- Full bed containment solutions
- Perimeter sealing solutions
- Easy to install
- Panels are designed to pass easily through the manway
- Can be fabricated in perforated plate, profile wire or wire mesh, all offering years of worry-free operation
- Can be installed over existing grating systems
- Easy choice for upgrading or replacing mesh over grating applications
- Designed for easy maintenance and cleaning
- Can be done in any thickness or material type needed
Can be designed for very high catalyst loading and high delta P
Horizontal Support Grids
-
- Great for applications requiring special filtration or separation
- Designed for application over existing grating or can be designed for a complete revamp to update and upgrade the SRU to meet the demands of the current process needs
- Hydraulic manipulation achieved with precision perforation coupled with a ridged inverted “C” channel design
- Can be fabricated in perforated plate, profile wire or wire mesh, all offering years of worry-free operation
- Can be done in any thickness or material type needed
Easy choice for Sulphur Recovery Unit (SRU) upgrading or replacement sections

Inlet Distributors (or Diffusers)
From the very simple slotted pipe inlet diffuser to licensor engineered inlet diffusers, WMP can fabricate the solution you need. With many styles and options, we are a one-stop-shop solution provider with years of experience in inlet diffusers.
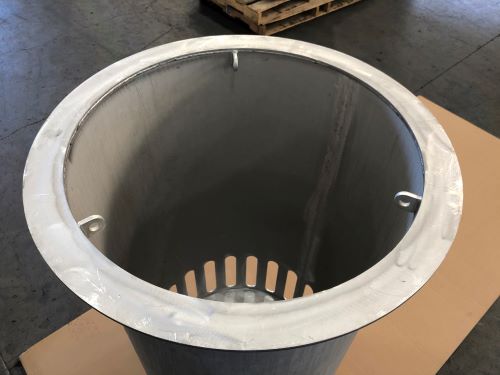
Catalyst Hold-Down/Floating Screens
Catalyst Hold-Down or Floating Screens help contain the catalyst bed or selected media while aiding in distribution of the feed. They also minimize catalyst bed upsets during any up-flow condition or regeneration cycles that the vessel may be subject to during its operation.
WMP offers a variety of options for catalyst hold-down / floating screens, including:
Perforated Plate Catalyst Hold-Down/Floating Screens
These screens are a great choice for catalyst beds that need additional distribution support to ensure full bed utilization, often overlooked in de-bottlenecking options. Read more about WMP’s Perforation Capabilities.
Common materials include carbon steel, all grades of stainless steel, and other high alloy materials.
Benefits include:
- Unlimited options and patterns to facilitate proper media retention/hold down and feed/flow distribution requirements
- Robust design, turnkey solution for optimizing and utilizing full bed distribution, while reducing or eliminating channeling or cone effects within the catalyst bed
- Easy to install or remove
- Very short lead time item
- Easy to clean
- Easy to handle, manway installable sections manufactured and labeled to fit the vessel
- WMP offers multiple hardware options for a variety of styles and needs
Profile Wire
These hold down/floating screens have similar design characteristics as perforated plate screens except for a continuous slot opening to facilitate proper media retention/hold down and feed distribution requirements. Profile wire is a great choice for catalyst beds that need additional distribution support to ensure full bed utilization, often overlooked in de-bottlenecking options.
Common materials include all grades of stainless steel and other high alloy materials.
Benefits include:
- Turnkey solution for optimizing and utilizing full bed distribution, while reducing or eliminating channeling or cone effects within the catalyst bed
- Easy to install or remove
- Easy to clean
- Easy to handle, manway installable sections manufactured and labeled to fit the vessel
- WMP offers multiple hardware options for a variety of sizes and needs
Wire Mesh/Wire Cloth
These are commonly used as a quick catalyst bed hold-down option when bed distribution and process de-bottlenecking are not required or considered.
Common materials include all grades of stainless steel, other high alloy materials, plastics, glass and Teflon.
Benefits include:
- Easy to handle, manway installable rolls are unrolled inside the vessel to fit parameters
- Very short lead time item, typically same-day order availability
- Easy to install and replace
- Typically, lower cost
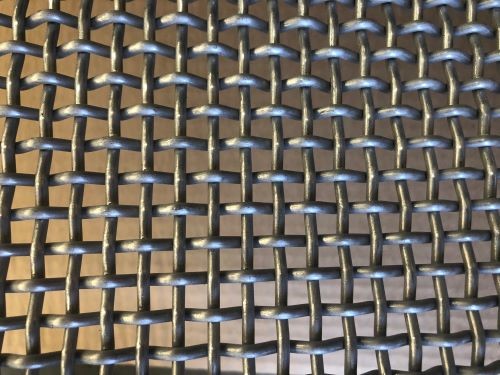
Trays
Depending on the process requirements, our team will fabricate new engineered solutions or complete as-built replacement trays or individual sections/panels within the tray. With many common materials in stock or readily available, we can promptly address all your fabrication needs.
Types of trays we offer for axial reactors include:
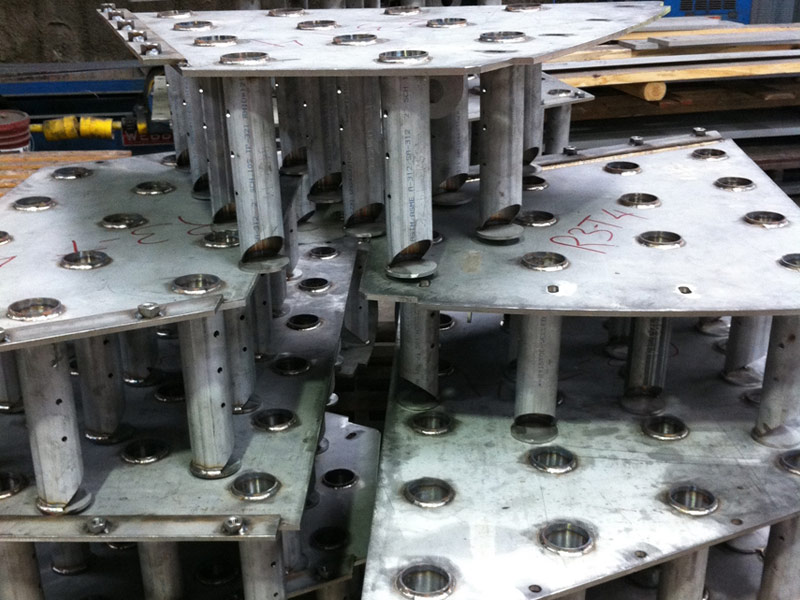
Distributor Tray
The most common in a reactor tray system, these can be standalone trays or used in concert with other trays. If used with other trays, distributor trays are usually the last step in the flow process. These trays are extremely important to creating an even flow before the feed is sent to the catalyst below, to optimize the process. Tolerances and metallurgy are extremely critical because of the high precision needed due to the various feeds and temperatures present in the process, as well as the desired utilization of the catalysts. WMP understands these needs and has serviced licensors and end-users for years, meeting the most difficult requirements in the industry.
Mixer Tray
In hydroprocessing reactors, mixing is required between catalyst beds, and equal mixing is important to ensure efficiency and proper utilization. Our team understands this process and takes steps necessary to manufacture uniform and precise mixing trays.
Quench / Quench Zone Tray
These trays are used for adding an agent or another product to the feed, and it’s imperative that the tray is uniform to allow for proper mixing. WMP routinely manufactures precise quench trays for a variety of processes.
Scale Catching Tray
This tray is used to catch trash or waste product, even the smallest of particles, which is critical to ensure no waste particles transfer to the catalyst bed. WMP understands this process and manufactures precise scale catching trays that can extend the life of the reactor process.
Support Beams
Regardless of the beam construction required, the WMP team has the equipment and expertise to provide a solution for your catalyst containment needs. Support beams are integral to hold up the catalyst support grids, which help seal each edge with a perfect fit along the vessel wall, ensuring catalyst is contained and not lost downstream.
Our team has many years of experience with various configurations of T-beams, inverted T-beams, Open Web (lattice beams) and I-beams to name a few.
We use multiple welding techniques, often using submerged arc, gas tungsten arc and other welding processes for our support beams. With our wide range of in-house machining capabilities and overhead crane capacity, we can easily manage projects and beams of any size.
Matched with WMP engineering and support grid system fabrication, WMP can fit beams and grids together for complete pre-installation fit-up, making installation in the field easier.
Our close relationships with numerous suppliers and mills give us access to a wide range of material and construction options, as well as the ability to complete tight turnaround times, making WMP a clear choice for support beam fabrication.
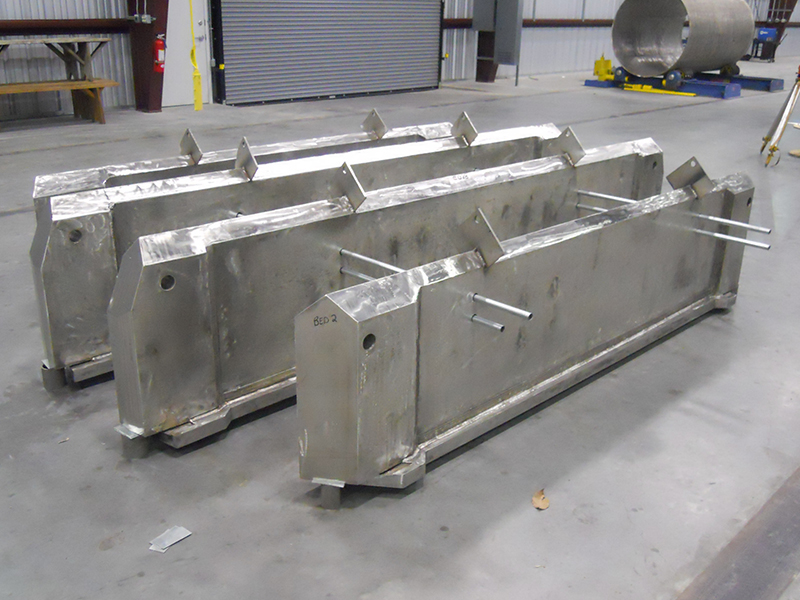
Headers & Laterals Systems
WMP designs and fabricates header and lateral systems to provide efficient full bed utilization and containment solutions. We can create engineered or replacement-in-kind solutions to optimize specific process conditions.
We offer headers and lateral systems across all material types, in multiple configurations, including profile/wedge wire, spray nozzle, pipe and tube, or other designs.
One popular method is profile/wedge wire, available in both header-lateral and hub-lateral assemblies. These can be connected to distributor headers and spider hubs in a variety of ways such as fabricated flanges, fully welded assemblies and more.
Benefits of profile/wedge wire include:
- Continuous flow design increases open area for even distribution
- Highly resistant to clogging
- Longevity, due to strength, with flexible design options
- Easy to clean and maintain
- Various types and sizes available
There are a variety of options including perforated plate, profile wire and precision cut and/or formed pipe.
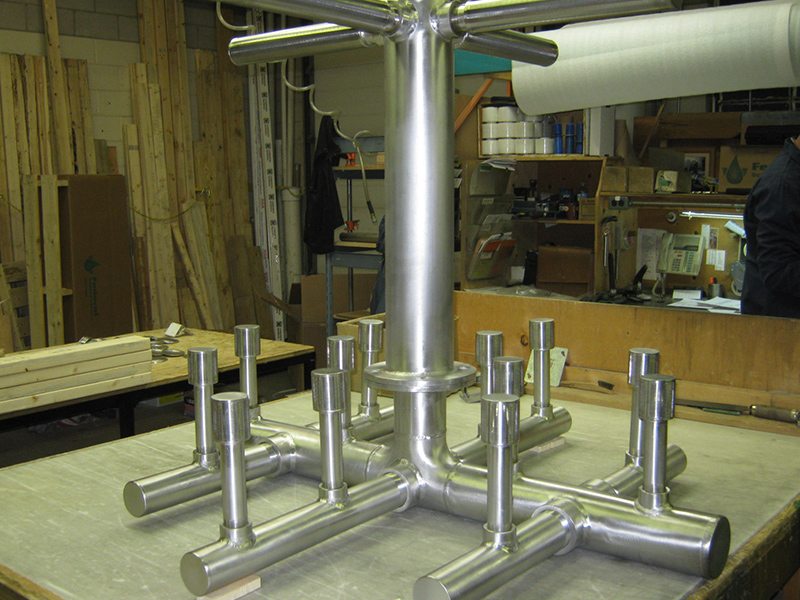
Outlet Collectors / Elephant stools
The WMP team has experience fabricating many engineered solutions for outlet collectors and elephant stools. Multiple options are possible.
- Paired with WMP support grid options, the outlet collector can be a key secondary containment solution in addition to flow devices
- Variety of top designs available from solid plate to perforated plate
- Easy to install with splitting options in the design
- Multiple mounting options offered including bolted, welded tab and welded pipe
- Vortex breakers can be included to optimize flow
- Perforated plate, wire mesh or profile wire exterior wrap options can be utilized depending on strength and pressure drop requirements
Axial / Downflow Reactor Specialty Products
We offer a variety of additional, specialty products for axial reactors, including:
- Hold-down hardware
- Other specialty hardware and packing types, such as:
- J-bolts and other grid hold down options
- Rope packing in many diameters, in stock and ready for quick shipment
- Gasketing, clips, pins and other common and specialty hardware in many sizes, in stock and ready for quick shipment
APPLICATIONS
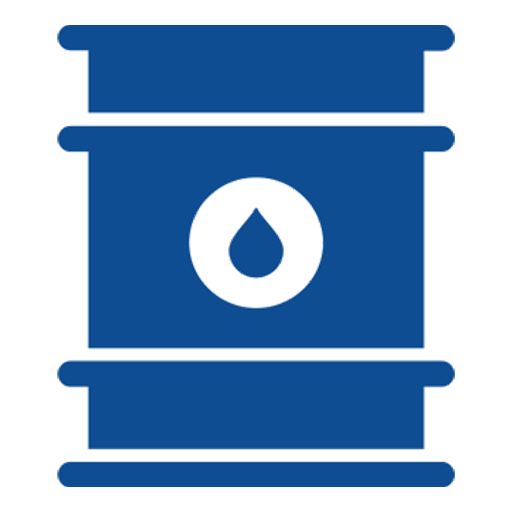
Oil & Gas
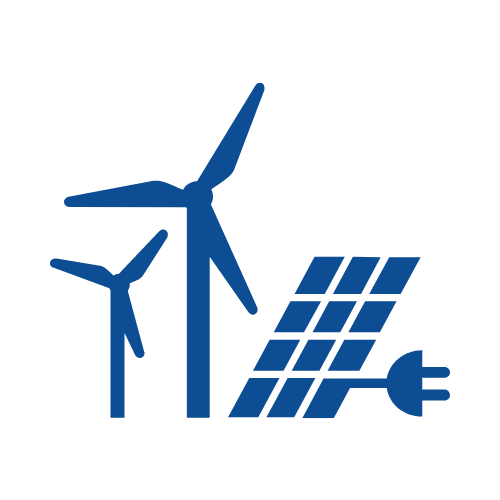
Renewable Energy
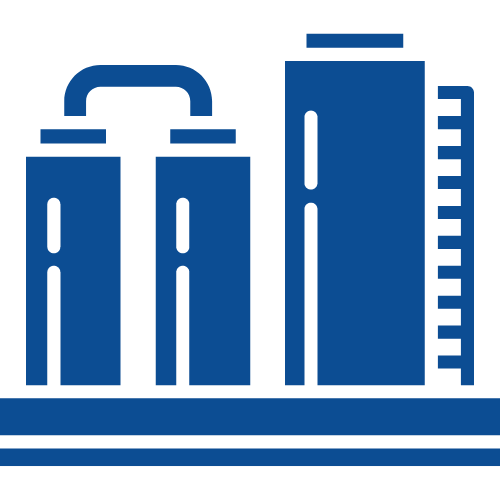
Chemical / Petrochemical
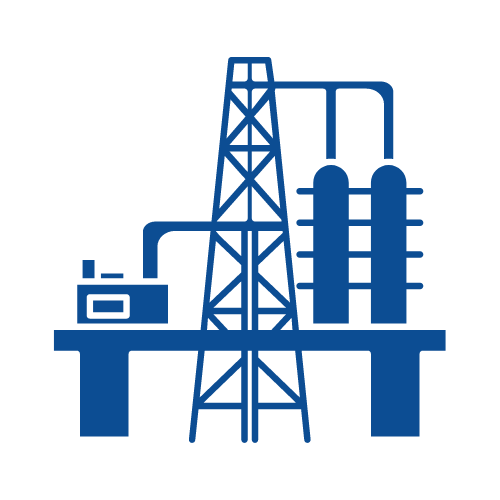